On April 22, 2024, Hebei Economic Daily carried a front-page report on Hebei Yanming Chemical Equipment Co., Ltd.
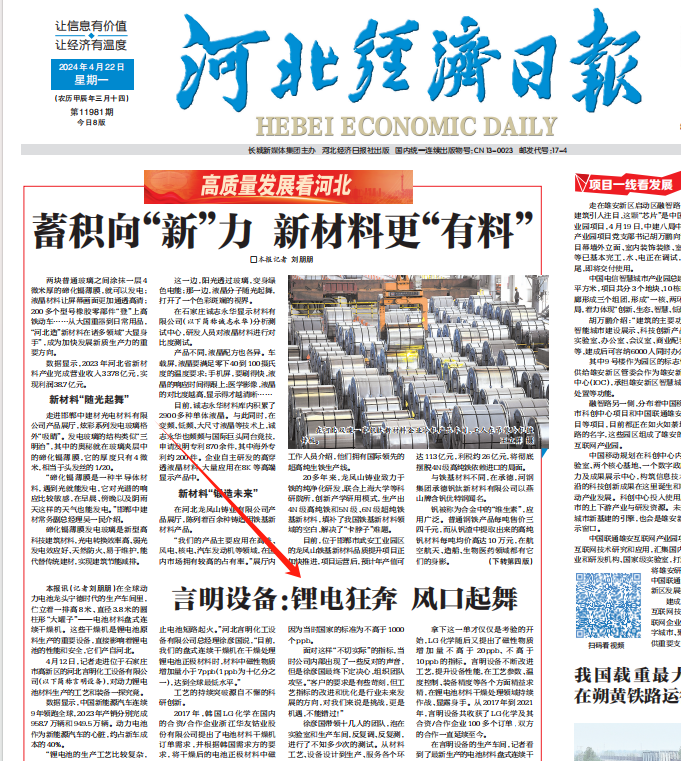
Here are the details of the report.
In the production workshop of Ningde era, the global power battery leader, stands a row of cylindrical "big jars" with a height of 8 meters and a diameter of 3.8 meters-disc continuous dryer for battery materials. These dryers are important equipment for the production of lithium battery raw materials, which directly affect the performance and safety of lithium batteries. They are produced in Hebei.
In the production workshop, the staff explained the internal structure of the disc continuous dryer. Hebei Economic Daily reporter Liu Pengpeng photo
On April 12, the reporter walked into Hebei Yanming Chemical Equipment Co., Ltd. (hereinafter referred to as Yanming Equipment) located in Shijiazhuang High-tech Zone to explore the technology and equipment for the production of power lithium battery materials.
Data show that China's new energy vehicles have led the world for nine consecutive years, with production and sales of 9.587 million and 9.495 million vehicles respectively in 2023. As the heart of new energy vehicles, power batteries account for about 40% of the cost of new vehicles.
"The production process of lithium batteries is relatively complicated. The drying of battery cathode materials is a key link in battery production, which can effectively reduce metal foreign matter and prevent battery short-circuit fires." Xu Yanguo, general manager of Hebei Yanming Chemical Equipment Co., Ltd., said, "At present, when our disc continuous dryer dries lithium battery cathode materials, the increase in magnetic substances in the materials is less than 7ppb(1ppb is one billionth), reaching The lowest level in the world."
The continuous breakthrough of the process comes from unremitting scientific research and innovation.
In 2017, South Korea's LG Chemical's joint venture/cooperative enterprise Zhejiang Huayou Cobalt Co., Ltd. put forward an order for a battery material dryer. According to the requirements of the South Korea demander, the increase in magnetic substances in the dried battery cathode material was set at no more than 50ppb. After seeing the customer's demand, Xu Yanguo made a mistake because the national standard at that time was no more than 1000 ppb.
Faced with such "unrealistic" indicators, there were some voices of opposition within the company at that time, but Xu Yanguo finally made up his mind to organize a team to tackle tough problems. "The customer's requirements are somewhat harsh, but the improvement and optimization of process indicators is the inevitable direction of the future development of the industry. It is a challenge for us, but also an opportunity, and we cannot let it go!"
Xu Yanguo led a team of more than a dozen people to soak in the laboratory and production workshop, repeatedly adjusted and tested, and conducted an unknown number of tests. From material technology, equipment design to production and service, it has been engaged in all aspects for more than a year, and finally reached the customer's standard, and the order was delivered smoothly.
Winning this order is only the beginning of the test. LG Chem then put forward the index that the increase of magnetic substances should not be higher than 20ppb and not higher than 10ppb. Yanming equipment continues to improve the process, improve equipment performance, in the process parameters, temperature control, equipment accuracy and other aspects of excellence, in the field of lithium battery material drying and continuous combat, show their skills. From 2017 to 2021, Yanming Equipment received more than 100 orders from LG Chemical and its joint venture/cooperative enterprises, and the cooperation between the two sides has continued to this day.
In the production workshop, workers are debugging equipment. Hebei Economic Daily reporter Liu Pengpeng photo
In the production workshop of Yanming equipment, the reporter saw the newly produced disc-type continuous dryer for battery materials, which was gently scratched with the tip of his finger in the internal stack, smooth and unhindered. It is understood that the contact material parts finish (surface roughness) can reach below Ra0.2.
"We have become one of the main process and equipment providers in the global lithium battery new energy industry for drying, evaporation, crystallization, carbonization and purification processes." Xu Yanguo said that Yanming equipment is a global leader in lithium battery cathode material precursor and lithium salt disc continuous dryer technology and equipment.
Continuously expand the "circle of friends" and expand the "business circle". At present, Yanming Equipment has established cooperative relations with more than 200 enterprises such as Ningde Times, BYD, Minmetals Salt Lake, Huayou Cobalt Industry, Pilot Materials, Sinochem Lithium, BASF, Yabao Chemical, LG Chemical, Rongjie, Guanghua Technology, etc., and has emerged in the global lithium new energy industry.
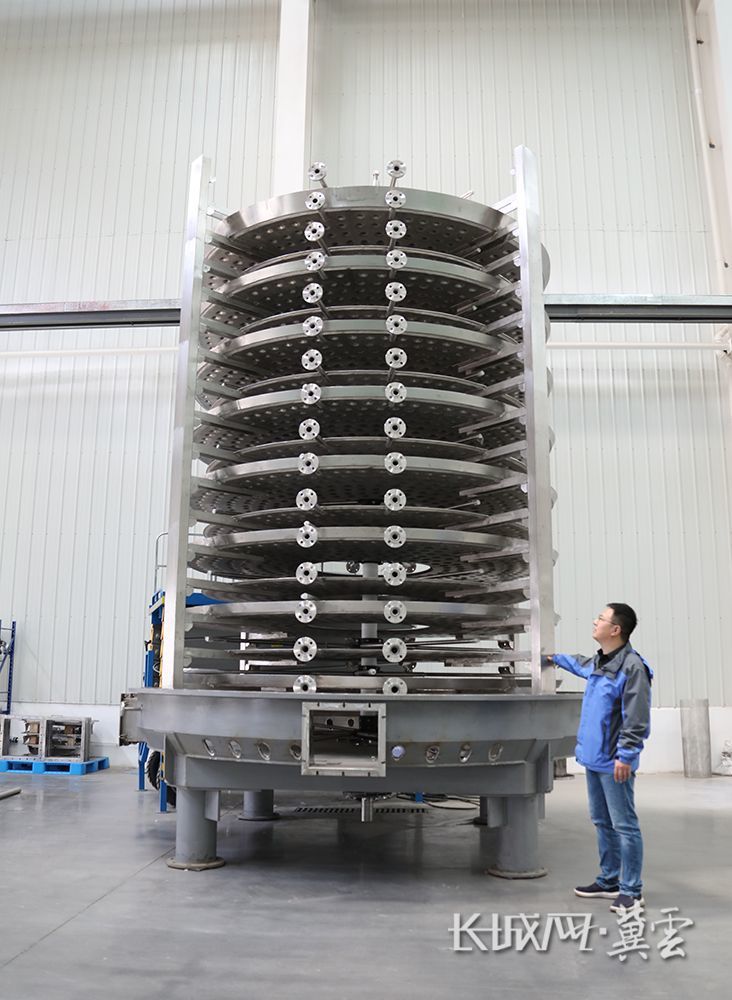
In the production workshop, workers are wiping equipment. Hebei Economic Daily reporter Liu Pengpeng photo
In recent days, the news about solid-state batteries "wave again", attracted the attention of Xu Yanguo.
"The solid-state battery of new energy vehicles removes the liquid electrolyte and uses the solid electrolyte, which is safer. Its energy density is also greater and its endurance is stronger, reaching 1,000-1,300 kilometers." Xu Yanguo said that in the production process, the negative electrode of all-solid-state lithium metal batteries can use lithium metal different from the existing mainstream carbon materials. "In the development of the front-end production process line of lithium metal, we will be committed to the optimization of the entire production line of lithium chloride concentration, crystallization, filtration, and drying, and the optimization of technologies such as the separation of lithium chloride and sodium chloride."
In the field of lithium battery materials, the equipment wants to do better and more.
With the explosive growth of new energy vehicles, the "retirement tide" of power batteries is also coming. As the "last mile" of the new energy vehicle industry chain, a new track for power battery recycling is emerging. As an "old man" who has been engaged in the development and design of equipment and technology in the lithium-ion new energy industry for 21 years, Xu Yanguo developed the continuous carbonization and purification technology of crude lithium carbonate earlier, and is widely used in domestic crude lithium carbonate and waste battery lithium salt purification to produce battery-grade high-purity lithium carbonate.
"Power battery recycling not only has ecological value, but also has market value. It is a direction for us this year." Xu Yanguo said that this year the company will focus on increasing research and development investment in improving the purity and recovery rate of lithium extraction from used batteries, helping to form an industrial closed loop of "battery production-use-echelon utilization-recycling and recycling.
Source: Hebei Economic Daily